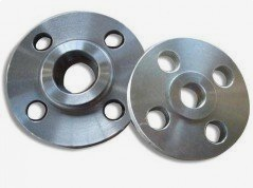
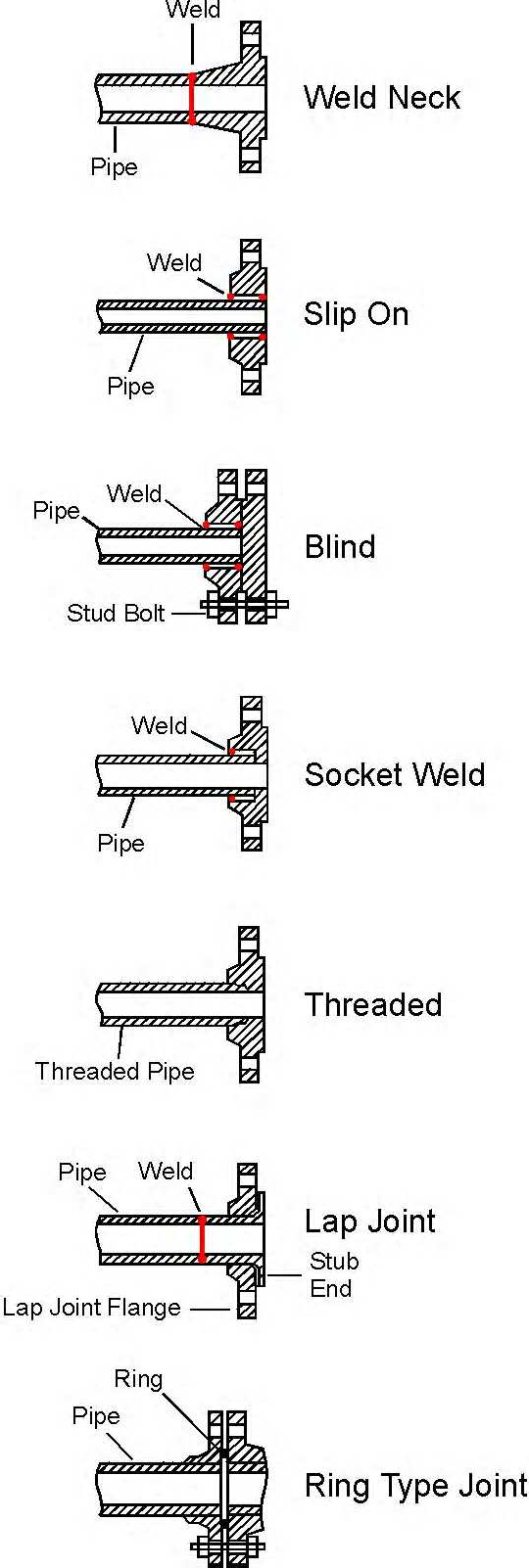
Type | Stainless steel flange,Carbon steel flange,Socket Weld Flange |
Standard | ASME,ANSI,DIN,JIS,BS |
Material | Stainless steel,Carbon steel |
Pressure | Class(150lb-1500lb) |
Size | 1/2"-24" |
Surface | Anti-rust Oil, Transparent/Yellow/Black Anti-rust Paint, Zinc Galvanized, Flame plating |
Applications | Petroleum, chemical, power, gas, metallurgy, shipbuilding, construction, etc |
Package | Standard export package,wooden case |
Payment item | L/C, T/T, D/P, Western Union, Paypal, Money Gram |
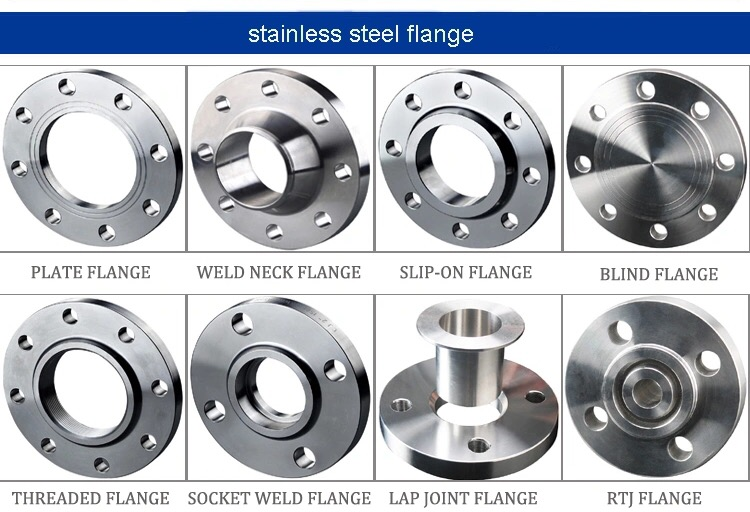
Socket welding flange refers to the flange in which the end of the pipe is inserted into the flange ring step and welded on the pipe end and the outside. There are two types with and without neck. The flange with neck pipe has good rigidity, small welding deformation and good sealing performance, and can be used in the occasions where the pressure is 1.0~10.0MPa. Type B flanges for containers are also socket welding flanges, which are used in occasions with high sealing requirements. When designing, the socket welding flange can be checked according to the integral flange.
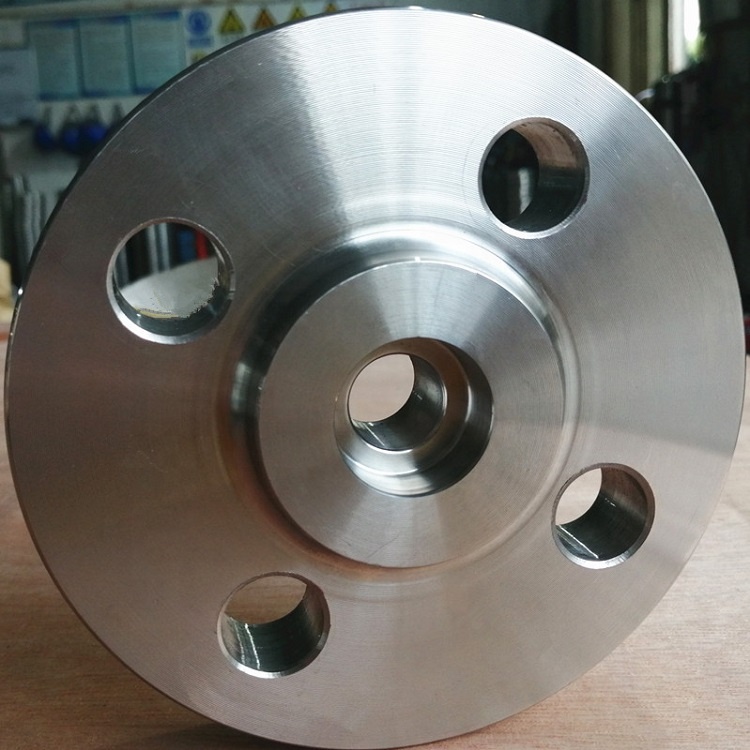
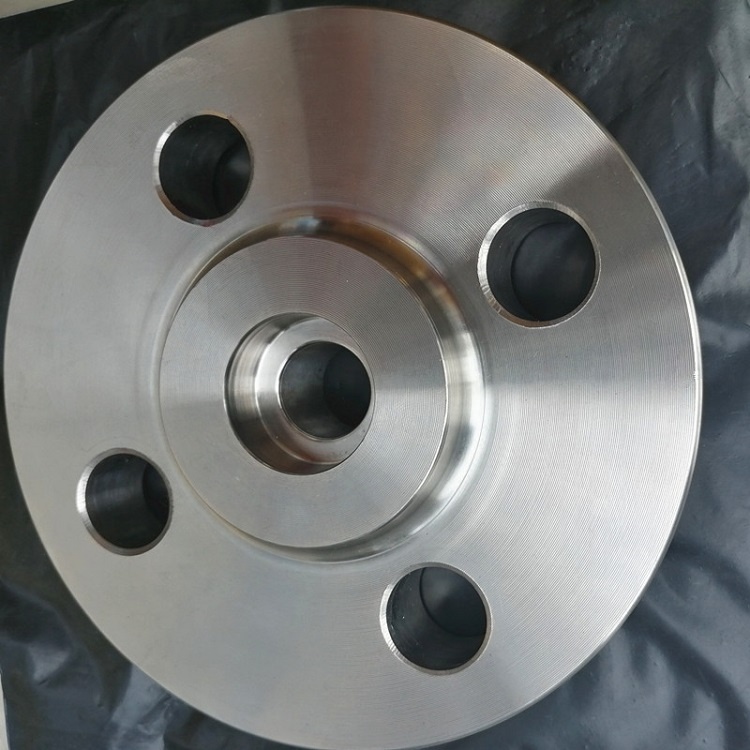
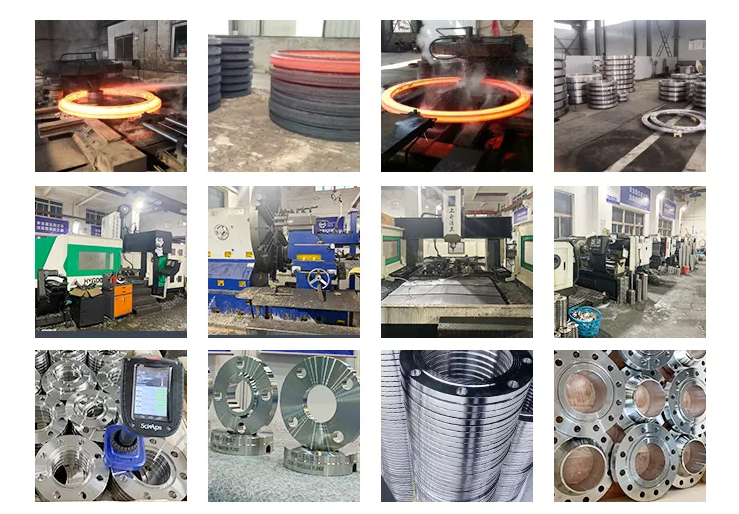
Socket welding is usually used for small pipes smaller than DN40 in diameter and is more economical. Socket welding is the process of first inserting a socket and then welding (for example, there is a type of flange called a socket flange, which is a projection weld flange, which is a connection when connecting to other parts, such as valves. Socket welding Usually the pipe is inserted into the flange and welded. Socket welding can be used for magnetic particle or penetration testing (carbon powder, penetrating carbon steel such as stainless steel) and is recommended if the fluid in the pipe does not require high welding requirements Socket welding, the type of connection that is easy to detect is mainly small-diameter valves and pipes, which are used for pipe joints and pipe welding. Small-diameter pipes usually have thin walls, which are prone to edge dislocation and ablation, and are difficult to butt welding, suitable for socket welding. Socket weld and socket. Welded sockets are often used under high pressure due to their reinforcing effect, but socket welding also has disadvantages. One is that the stress state after welding is not good, and it is difficult to completely melt. Trends are: piping systems with gaps and therefore unsuitable for crevice corrosion-sensitive media and piping systems with high cleanliness requirements; the use of socket welds; and ultra-high pressure piping. Large wall thicknesses are available even in small diameter pipes, and socket welds can be avoided as much as possible by butt welding.