Product Description
The slip on flange, like the plate flat welding flange, is also a flange that extends the steel pipe, pipe fittings, etc. into the flange and connects with the equipment or pipeline through the fillet weld. The slip on flange is also a flat welding flange, because there is a short neck, which increases the strength of the flange and improves the bearing capacity of the flange. So it can be used on higher pressure pipelines.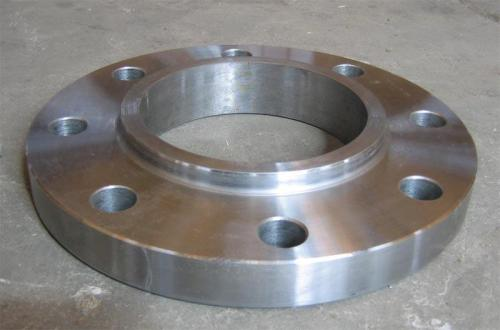
Main Connection Size of Slip On Flange
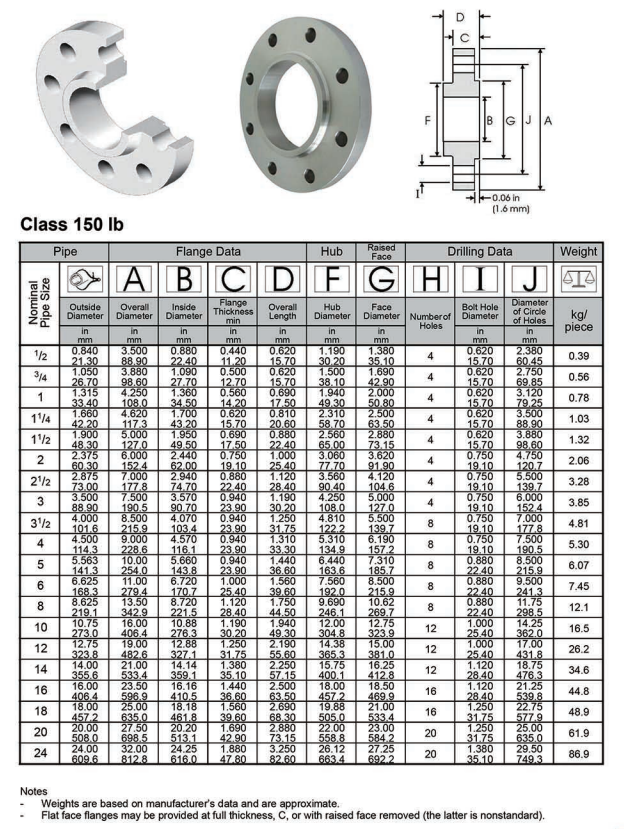
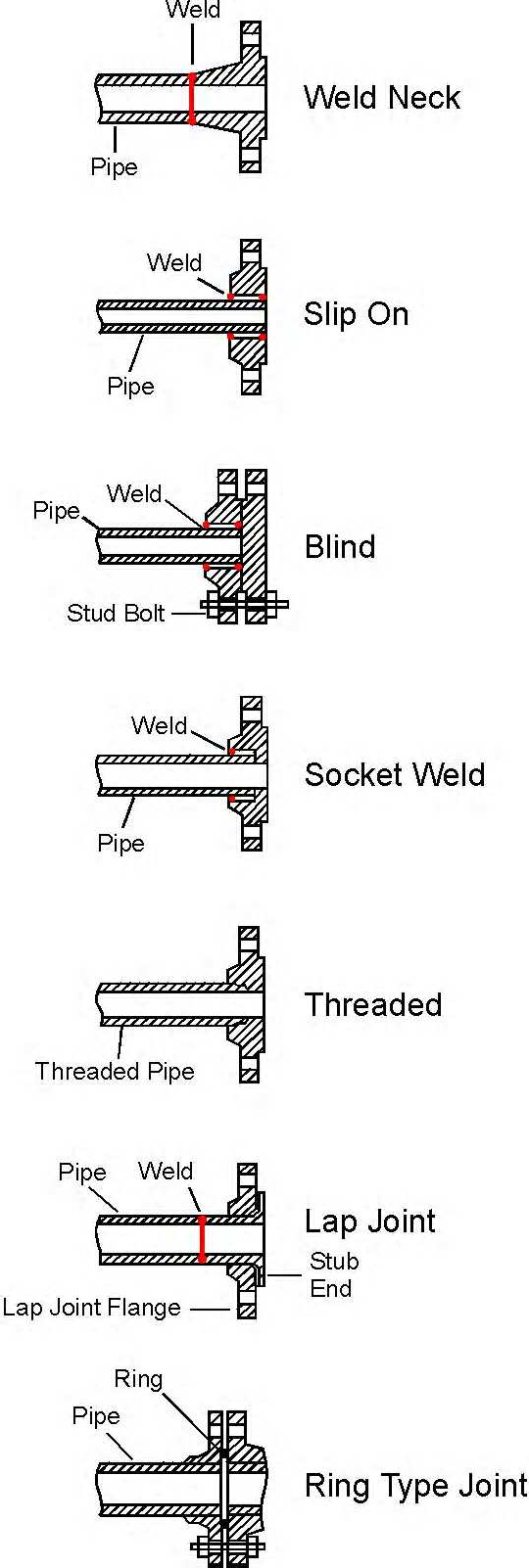
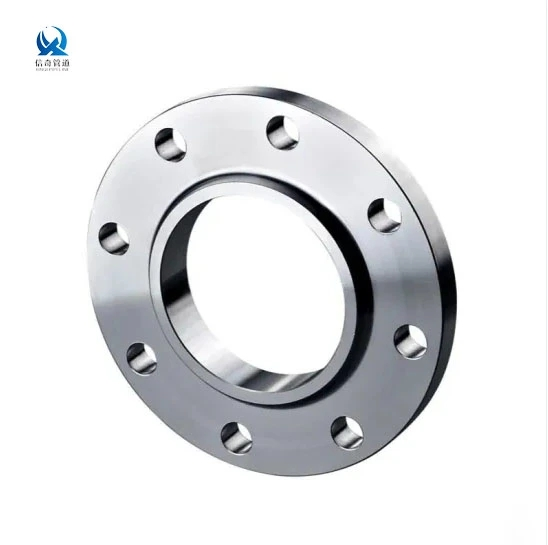
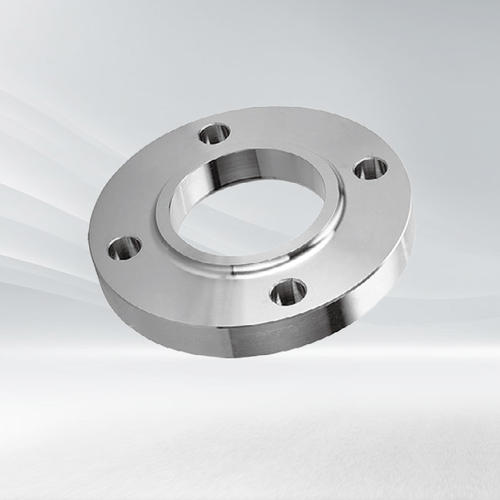
Size | ASME B16.5:1/2"-24" ASME B16.47:26"-48" |
Rating | 150lb/300lb/600lb/900lb/1500lb/2500lb |
Standard | ASME B16.5,ASME B16.47A,ASME B16.47, MSS SP 44, DIN 2632, DIN2633, DIN2634, DIN2635, DIN2636, JISB2220, BS4504, GB, etc |
Material |
|
Surface | Black Painting / Anti Rust Oil / Hot Dip Galvanized |
Certification | ISO 9001:2015 |
Port of delivery | Tianjin Port |

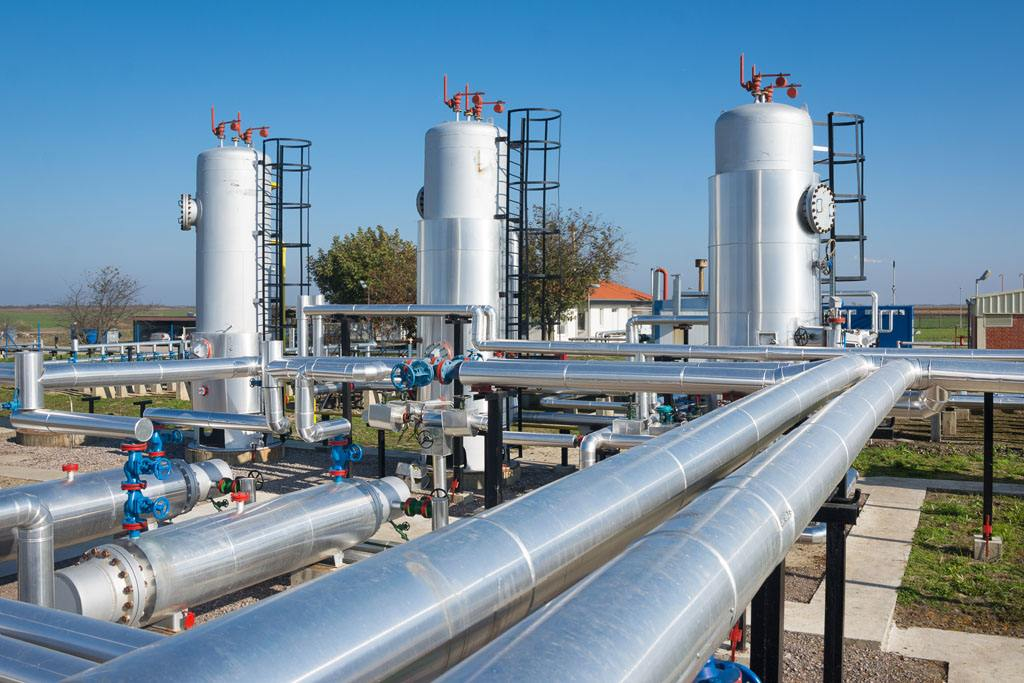
The difference between SO and WN
1. The welding seam forms are different:
Flat welded seams cannot be radiographically inspected, but butt welded seams can. The welding seam form of the necked flat welding flange pipe and the flange is a fillet weld, while the welding seam form of the neck butt welding flange and the pipe is a girth weld; the flat welding is two fillet girth welds, A butt weld is a butt girth weld. The difference between the flat welding flange with neck and the flat welding flange without neck is that the flat welding flange with neck is one more place in the pipeline welding part than the flat welding flange without neck. The flange is also a flat flange, and the boss without flange is also a flat fillet weld. The weld between the necked butt welding flange and the connecting pipe belongs to the B-type seam, and the weld between the necked butt-welding flange and the connecting pipe belongs to the C-type seam, and the non-destructive testing after welding is different.
2. The nominal pressure is different:
The nominal pressure of the necked flat welding flange is: 0.6---4.0MPa, while the nominal pressure of the necked butt welding flange is: 1--25MPa level, obviously, the necked flat welding flange The adaptive pressure level is lower.
3. Different connection methods:
The biggest difference in structure between the necked flat welding flange and the necked butt welding flange is the connection between the nozzle and the flange. The necked flat welding flange is generally a nozzle and a flange corner connection. , And the butt welding flange with neck is the butt joint between the flange and the nozzle.
Flat welding flanges can generally only be connected to pipes, not directly to butt welded pipe fittings; butt welded flanges can generally be directly connected to all butt welded pipe fittings (including elbows, tees, reducers, etc.), of course Also includes pipes.
The stiffness of butt welding flange with neck is higher than that of flat welding flange with neck, and the strength of butt welding is higher than that of flat welding, and it is not easy to leak.
Welding neck flanges and butt welding neck flanges cannot be replaced casually. From the manufacturing point of view, the welding neck flanges (SO is the abbreviation of SLIP ON) have a large inner diameter, which means low weight and low cost. In addition, the nominal diameter Neck butt welding flanges (WN is the abbreviation of WELDING NECK) larger than 250mm need to be tested, SO flanges do not need to be tested, so the cost is relatively low.
Flat neck welding is used more in imported oil installations, similar to the American standard S0, butt welding flange with neck is used for highly hazardous media.
Advantages and Disadvantages
Advantages: Flat-welded flanges with necks are also flat-welded flanges, because there is a short neck, which increases the strength of the flange and improves the bearing capacity of the flange. So it can be used on higher pressure pipelines.
Disadvantages: Compared with the plate-type flat welding flange, the cost is higher, and it is easier to bump during transportation due to its shape characteristics.